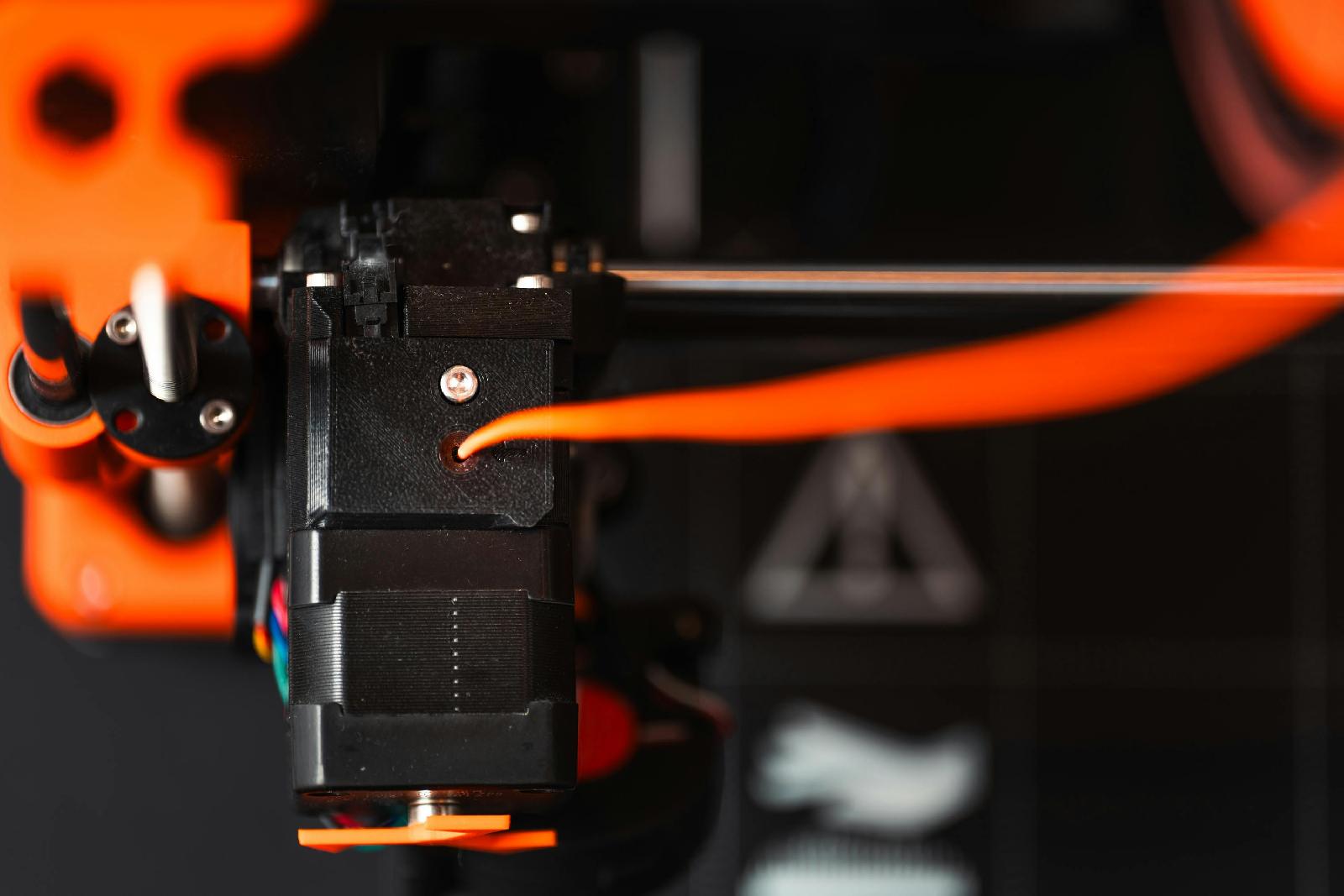
Dans l’univers de la production industrielle, le moulage par injection plastique représente une technique fondamentale pour la fabrication de composants précis et complexes. Chaque élément du moule joue un rôle déterminant dans la qualité finale des pièces produites. Cet article visite en profondeur les différents composants essentiels qui constituent un moule d’injection plastique moderne.
Les fondamentaux d’un moule d’injection et ses principales sections
Un moule d’injection plastique est bien plus qu’un simple réceptacle pour matière fondue. Il s’agit d’un assemblage précis de multiples composants techniques travaillant en synergie. La connaissance approfondie de ces éléments permet aux ingénieurs et techniciens de concevoir des moules plus performants et d’optimiser la production.
Les moules d’injection se divisent fondamentalement en deux sections principales : la partie fixe (côté A) et la partie mobile (côté B). La partie fixe reste attachée à la plaque stationnaire de la presse à injecter, tandis que la partie mobile se déplace pour permettre l’ouverture du moule et l’éjection des pièces finies.
La partie fixe du moule d’injection plastique contient généralement le système d’alimentation en matière plastique, comprenant la busette d’injection qui reçoit le polymère fondu de la presse. Cette section abrite également une partie de la cavité qui donnera forme à la pièce finale.
De son côté, la partie mobile du moule intègre le système d’éjection et souvent des noyaux qui formeront les caractéristiques internes de la pièce. L’interface entre ces deux parties constitue le plan de joint, élément crucial pour la qualité des pièces produites.
Les différents types de moules d’injection
Selon les besoins de production et la complexité des pièces, plusieurs configurations de moules peuvent être utilisées :
- Moules à deux plaques : configuration la plus simple avec une seule ligne de séparation
- Moules à trois plaques : permettant une séparation du système d’alimentation
- Moules familiaux : produisant plusieurs pièces différentes en un seul cycle
- Moules à dévissage : pour les pièces comportant des filetages
- Moules multi-injection : permettant l’injection de plusieurs matériaux
Systèmes fonctionnels essentiels d’un moule d’injection
Pour transformer efficacement la matière plastique en pièces finies, un moule d’injection intègre plusieurs systèmes techniques spécialisés. Chacun remplit une fonction précise et contribue à la qualité du produit final.
Le système d’alimentation constitue la porte d’entrée du plastique fondu dans le moule. Il comprend la carotte d’injection (point d’entrée du plastique), les canaux de distribution (runners) et les seuils d’injection (gates). Ces éléments peuvent être de type « canal froid » où la matière se solidifie à chaque cycle, ou « canal chaud » maintenant la matière à l’état fondu grâce à des résistances chauffantes.
Le système de refroidissement joue un rôle crucial dans le cycle de production, représentant jusqu’à 80% du temps total. Un réseau de canaux permet la circulation d’un fluide caloporteur (généralement de l’eau) autour des empreintes du moule. La conception optimale de ce système influence directement la productivité et la qualité des pièces.
Le système d’éjection permet de libérer la pièce solidifiée du moule. Il comprend principalement des éjecteurs (tiges métalliques), une plaque support d’éjecteurs et un mécanisme de retour. Ce système doit être conçu pour éviter toute déformation ou marque sur la pièce finale.
Le système de guidage assure l’alignement parfait des deux parties du moule lors de la fermeture. Il se compose de colonnes de guidage et de bagues qui garantissent une précision d’assemblage cycle après cycle, essentielle pour maintenir les tolérances dimensionnelles des pièces produites.
Un système d’évacuation d’air bien conçu prévient les défauts comme les brûlures ou les remplissages incomplets. De petits canaux d’évents permettent à l’air de s’échapper lorsque le plastique remplit la cavité, sans laisser sortir la matière.
Éléments structurels et choix des matériaux
Au-delà des systèmes fonctionnels, la structure même du moule détermine sa durabilité et ses performances dans des conditions d’exploitation industrielle exigeantes.
La base structurelle du moule comprend plusieurs plaques superposées qui forment un assemblage rigide. Ces plaques incluent les plaques de serrage, les plaques porte-empreintes, les plaques support d’éjecteurs et diverses plaques intermédiaires selon la complexité du moule.
Les empreintes et noyaux représentent le cœur fonctionnel du moule. Ces éléments, parfois interchangeables, définissent directement la géométrie des pièces produites. Ils sont conçus avec des angles de dépouille permettant le démoulage et bénéficient souvent de traitements de surface spéciaux pour résister à l’usure.
La sélection des matériaux pour les composants du moule s’avère déterminante pour sa longévité et ses performances. Les aciers les plus couramment utilisés incluent :
- Acier pré-traité (P20, 2311) pour les moules de moyenne série
- Acier à haute résistance (H13, 1.2344) pour les applications exigeantes
- Acier inoxydable pour les matières corrosives ou médicales
- Alliages d’aluminium pour les prototypes ou petites séries
- Alliages cuivre-béryllium pour une dissipation thermique optimale
Les éléments auxiliaires comme les systèmes de guidage, les bagues de centrage, les vis et les systèmes de manutention complètent l’ensemble. Ces composants standardisés facilitent la construction et la maintenance des moules tout en garantissant leur bon fonctionnement.
Optimisation et résolution des problèmes courants
La maîtrise des composants d’un moule d’injection permet d’anticiper et de résoudre efficacement les problèmes potentiels qui peuvent affecter la qualité des pièces produites.
Les défauts d’injection fréquents comme les lignes de soudure, les retassures, les marques d’éjection ou les déformations peuvent souvent être attribués à des problèmes spécifiques dans la conception ou le fonctionnement des composants du moule. Une analyse méthodique permet d’identifier la source du problème et d’y apporter une solution adaptée.
L’équilibrage des flux de matière représente un aspect crucial de la conception d’un moule performant. Un système d’alimentation bien conçu assure un remplissage uniforme de toutes les cavités, particulièrement important dans les moules multi-empreintes ou les pièces à géométrie complexe.
La gestion thermique optimale constitue souvent la clé d’un cycle de production efficace. Un système de refroidissement adapté aux caractéristiques de la pièce permet de réduire les temps de cycle tout en améliorant la qualité dimensionnelle des produits finis.
Les avancées technologiques comme la fabrication additive métallique, les capteurs intégrés ou les systèmes de contrôle numérique ouvrent de nouvelles perspectives pour la conception de moules toujours plus performants, répondant aux exigences croissantes de l’industrie moderne.